{{flagHref}}
Products
- Products
- Categories
- Blog
- Podcast
- Application
- Document
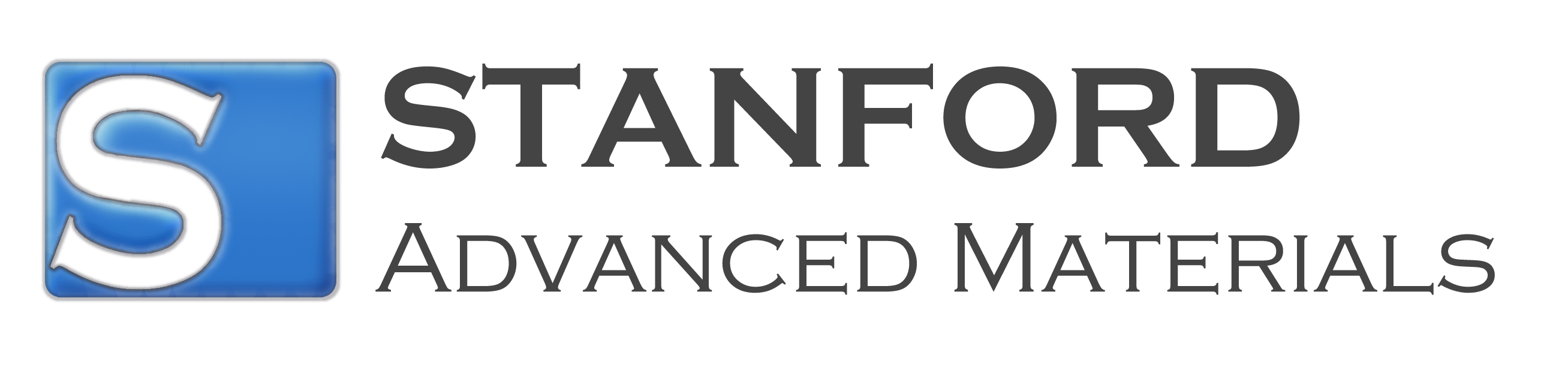
INDUSTRIES
Chemical & Pharmacy
Pharmaceutical Industry
Aerospace
Agriculture
Automotive
Chemical Manufacturing
Dentistry
Electronics
Energy Storage & Batteries
Fuel Cells
Investment Grade Metals
Jewelry & Fashion
Lighting
Medical
Oil & Gas
Optics
Paper & Pulp
Pharmaceuticals & Cosmetics
Plating
Research & Laboratory
Solar Energy
Space
Steel & Alloy Producers
Sports Equipment
Textiles & Fabrics
APPLICATIONS
Tungsten Applications
Metallurgy
Semiconductor
Rare-earth Magnets
Catalyst
3D Printing Powder
High Entropy Alloy Powder
Metal Injection Molding
Additive Manufacturing
Thermal Spraying Coatings
Hot Isostatic Pressing
Rare Earth Element Application
Environmental Catalysts
Marker Band
OLED Materials
Thermocouple Wire
Packing & Internals
Li-ion Battery & Electronic Chemicals
Metal Powders for Diamond Tools
Soft Magnetic Powder
-
- Chemical & Pharmacy
- Pharmaceutical Industry
- Aerospace
- Agriculture
- Automotive
- Chemical Manufacturing
- Dentistry
- Electronics
- Energy Storage & Batteries
- Fuel Cells
- Investment Grade Metals
- Jewelry & Fashion
- Lighting
- Medical
- Oil & Gas
- Optics
- Paper & Pulp
- Pharmaceuticals & Cosmetics
- Plating
- Research & Laboratory
- Solar Energy
- Space
- Steel & Alloy Producers
- Sports Equipment
- Textiles & Fabrics
-
- Tungsten Applications
- Metallurgy
- Semiconductor
- Rare-earth Magnets
- Catalyst
- 3D Printing Powder
- High Entropy Alloy Powder
- Metal Injection Molding
- Additive Manufacturing
- Thermal Spraying Coatings
- Hot Isostatic Pressing
- Rare Earth Element Application
- Environmental Catalysts
- Marker Band
- OLED Materials
- Thermocouple Wire
- Packing & Internals
- Li-ion Battery & Electronic Chemicals
- Metal Powders for Diamond Tools
- Soft Magnetic Powder